The True Cost of Blown-In Insulation for Your Home
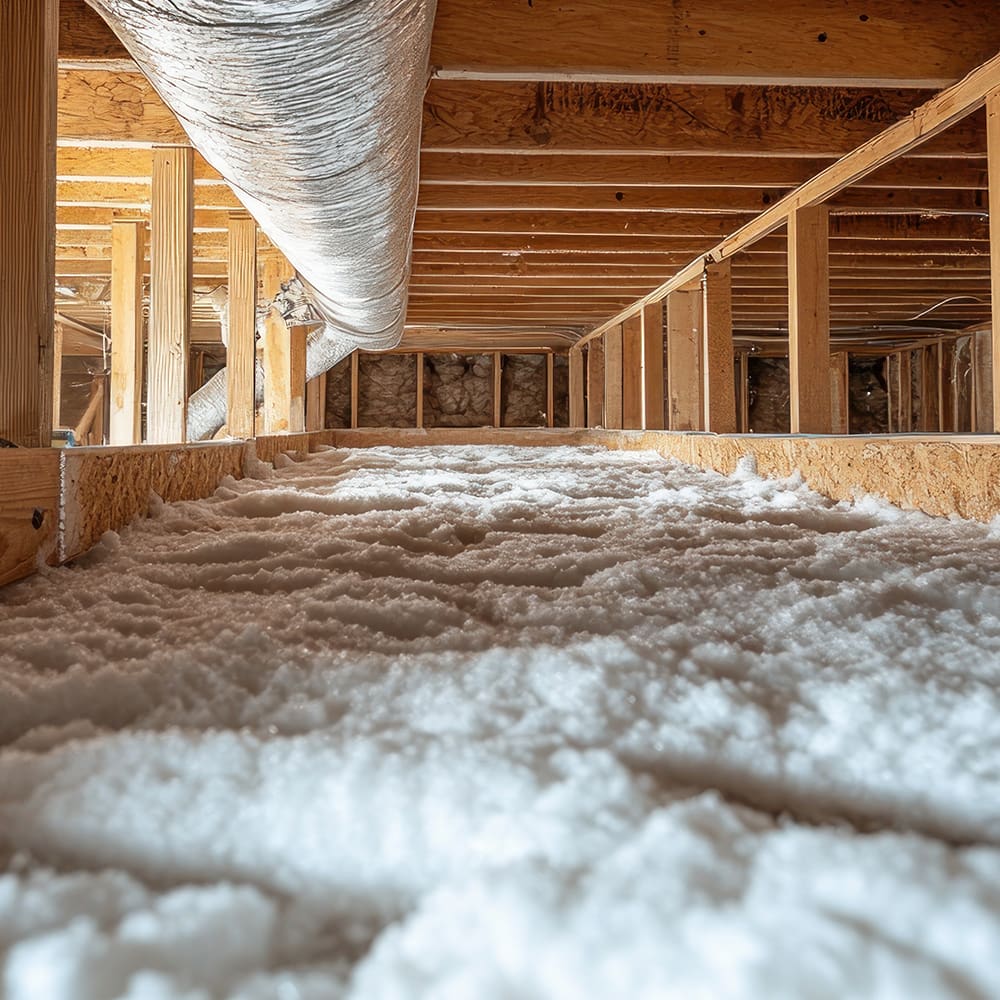
In home improvement projects, cost-efficiency and effectiveness are key considerations. Among various insulation options, blown-in insulation has gained popularity due to its versatility and relative ease of installation. But what does blown-in insulation cost, and is it worth the investment? This comprehensive guide will walk homeowners through the various aspects of blown-in insulation cost, including material options, installation process, and long-term benefits.
In this article
In home improvement projects, cost-efficiency and effectiveness are key considerations. Among various insulation options, blown-in insulation has gained popularity due to its versatility and relative ease of installation. But what does blown-in insulation cost, and is it worth the investment? This comprehensive guide will walk homeowners through the various aspects of blown-in insulation cost, including material options, installation process, and long-term benefits.
What is Blown-In Insulation?
Blown-in insulation, also known as loose-fill insulation, consists of small particles of fiber, foam, or other materials that are “blown” into attics, walls, and floor cavities. This method of insulation ensures even coverage and can reach nooks and crannies that are difficult for other types of insulation to cover.
Types of Blown-In Insulation
There are primarily three types of blown-in insulation materials—cellulose, fiberglass, and mineral wool. Each has its unique benefits and cost factors.
- Cellulose:
- Made from recycled paper products.
- Excellent for eco-conscious homeowners.
- Offers good thermal resistance.
- Fiberglass:
- Made from fine glass fibers.
- Resistant to moisture and mold.
- Generally less expensive than cellulose.
- Mineral Wool:
- Also known as rock wool, made from volcanic rock and minerals.
- Fire-resistant and soundproof.
- Higher cost but offers excellent durability.
Factors Affecting Blown-In Insulation Cost
Material Costs
The type of material you choose significantly impacts the overall cost. Cellulose and fiberglass are generally less expensive, ranging from $0.50 to $1.50 per square foot. Mineral wool, known for its superior properties, can cost between $1.00 and $2.00 per square foot.
Installation Costs
Professional installation costs vary based on the complexity of the job and regional labor rates. On average, homeowners can expect to pay between $1.50 and $3.00 per square foot for professional installation, inclusive of labor and materials.
Project Scope
The size and scope of your project play a crucial role in determining the total expenditure. Larger spaces will naturally require more material and labor, thus increasing costs. It’s essential to get an accurate measurement of the area you plan to insulate.
Benefits of Blown-In Insulation
Energy Efficiency
Blown-in insulation excels in sealing gaps and providing uniform coverage, which significantly reduces air leaks. This leads to lower energy bills, making your home more energy-efficient. According to the U.S. Department of Energy, proper insulation can reduce heating and cooling costs by up to 20%.
Soundproofing
The dense nature of blown-in insulation materials helps to dampen noise. This is particularly beneficial for homes located near busy streets or loud neighborhoods, providing a quieter indoor environment.
Fire Resistance
Certain materials like mineral wool provide excellent fire resistance. This added safety feature can be particularly appealing for homeowners looking to bolster their home’s protective measures.
Comparing Blown-In Insulation Costs to Other Types
Fiberglass Batts
Fiberglass batts are typically less expensive upfront, costing between $0.30 and $1.00 per square foot. However, they don’t offer the same level of coverage and efficiency as blown-in insulation, potentially leading to higher energy bills over time.
Spray Foam
Spray foam provides superior insulation but comes at a higher cost, ranging from $1.50 to $4.00 per square foot. While it offers excellent thermal resistance and air sealing, the higher initial investment may not be justifiable for some homeowners.
Reflective or Radiant Barriers
Reflective or radiant barriers are mainly used in attics to reduce cooling costs. They cost about $0.10 to $0.25 per square foot. However, they are not as effective in cold climates compared to blown-in insulation.
DIY vs. Professional Installation
DIY Installation
For the handy homeowner, renting insulation blowing equipment and purchasing materials can save money. Equipment rental typically costs around $100 to $200 per day. However, improper installation can lead to gaps and inefficiencies, negating potential savings.
Professional Installation
Hiring professionals ensures that the job is done correctly and efficiently. Professionals also offer warranties on their work, providing peace of mind. The added cost may be worthwhile considering the long-term savings and efficiency gains.
Long-Term Savings and Return on Investment (ROI)
Energy Bill Reductions
By reducing energy consumption, blown-in insulation can pay for itself within a few years through lower utility bills. This long-term saving is an essential factor to consider when evaluating the cost.
Increased Home Value
A well-insulated home is more attractive to buyers, potentially increasing the resale value. This makes blown-in insulation a smart investment for those looking to sell their homes in the future.
Tax Credits and Incentives
Various federal and state programs offer tax credits and incentives for homeowners who make energy-efficient improvements. It’s worth exploring these options to offset the initial investment.
Common Misconceptions About Blown-In Insulation
It’s Only for Attics
While attics are a common area for blown-in insulation, it’s equally effective in walls and floors, providing comprehensive thermal coverage for the entire home.
It’s Too Expensive
When considering the long-term energy savings and potential increase in home value, the initial cost of blown-in insulation is often outweighed by its benefits.
It’s Not Eco-Friendly
Modern blown-in insulation materials, especially cellulose, are manufactured from recycled products and are environmentally friendly, offering a sustainable insulation solution.
Preparing for Blown-In Insulation Installation
Assessing Current Insulation
Before installing blown-in insulation, assess your current insulation to determine if removal is necessary. Some materials can be topped up, while others may require complete removal.
Sealing Air Leaks
To maximize the effectiveness of blown-in insulation, ensure all air leaks are sealed. This includes areas around windows, doors, and electrical outlets.
Choosing the Right Contractor
Selecting a reputable contractor is crucial. Look for professionals with experience, positive reviews, and proper licensing to ensure a quality installation.
Conclusion
Blown-in insulation offers homeowners a cost-effective, efficient, and eco-friendly way to improve their home’s energy efficiency and comfort. By understanding the various factors affecting blown-in insulation cost and comparing it to other insulation options, homeowners can make an informed decision that best suits their needs and budget.